Checking and Truing a Planing Form
by Mike McGuire
I
was dissatisfied with my hand-filed planing form. It was a lot of
extra trouble to get good angles and dimensions especially with butt
strips. I suspected it was the angle of the groove. I had made it by
the usual method of setting a reverse taper. I filed with an
adjustable depth file plane, so that a dial indicator with a 60
degree point would indicate a constant depth over the whole length of
the form. The process is described in this article. It was an epic job, leaving me with an appreciation of
what life must be like for those Khyber Pass gunsmiths who turn out
whole AK47’s with just files and hand drills.
Checking
with a 60 degree fishtail/thread gauge didn’t show any problem. I
needed something better.
There is a method for setting the depth of
the form by laying a cylindrical rod of known diameter in the groove,
and measuring the height it stands proud of the groove.
I came up with a variation of this using rods of two different diameters to
measure the angle of the groove.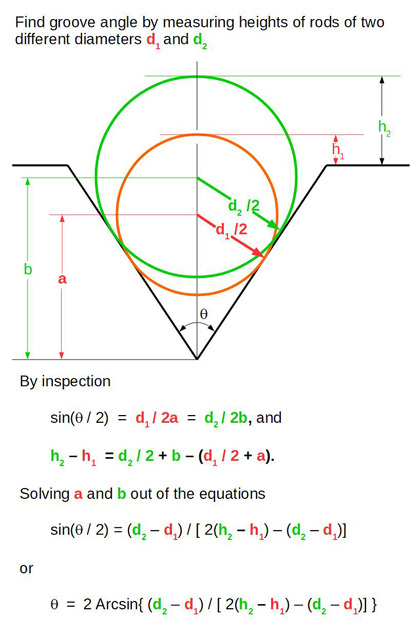
The
value of the sine of the half angle is 0.5 if the angle is a true
60 degrees. Arcsin is mathspeak for the "angle whose sine value is ..."
The
most convenient way to measure is with a dial indicator with a flat
point, in a fixture with a slot cut through it wider than the diameter
of the largest rod used. It is zeroed against the top of the form.
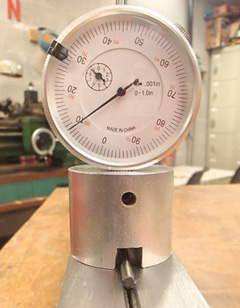
For
the rods I used drills from a good quality drill index. I mike'd them
all around and found that they were round to within a ten thousandth or
two, but were typically off a thousandth or so from their nominal
diameters, so I used the measured diameters in the computations.
I set the planing form to a constant depth, D
= 0.3125, at each station along its length. The filed depth of
the form was 0.085 at the first station and 0.155 at the last 70 inches
away.I decided to measure every 2.5 inches along the form. I
wanted the contact points of the rods at each station to be widely
spaced, the larger around 0.010 from the top of the groove and the
smaller 0.010 above the bottom . Thus I could use one drill to measure
all the stations at the top, but had to use an increasing progession of
sizes for the lower measurement as the depth of the groove became shallower.
The contact depth C determined by the rod diameter d, and the height is
C = 3d/4 - h
With the set depth D we have
D = 3d/2 - h
From these two equations we can eliminate h to get the rod diameter d required for a given C
d = 4(D - C)/3
For
the set depth D of 0.3125 and contact C around 0.010 the rod diameter d is
0.403. The closest drill in a 1/16 spaced set is 13/32 or 0.406 which
is what I used. I calculated this table to determine rod diameters and the expected heights for
the lower measurements of the groove.
Contact Depth |
Rod Dia |
h |
0.010 |
0.404 |
0.293 |
0.020 |
0.391 |
0.273 |
0.030 |
0.377 |
0.253 |
0.040 |
0.364 |
0.233 |
0.050 |
0.351 |
0.213 |
0.060 |
0.337 |
0.193 |
0.070 |
0.324 |
0.173 |
0.080 |
0.311 |
0.153 |
0.090 |
0.297 |
0.133 |
0.100 |
0.284 |
0.113 |
0.110 |
0.271 |
0.093 |
0.120 |
0.257 |
0.073 |
0.130 |
0.244 |
0.053 |
0.140 |
0.231 |
0.033 |
0.150 |
0.217 |
0.013 |
The results of the measurement were rather bad--an average of 68 degrees! I didn’t think taking the file plane to the groove was going to
improve it, as it likely caused the problem in the first place. I
took a half inch piece of hardwood about a foot long, to my table
saw. I set the blade over to 30 degrees away from vertical. I checked
this with a 30-60-90 drawing triangle rather than relying on the
scale on the saw. I made a cut the length of the piece of wood, and glued a 12”
long mill
file to the sloping cut with epoxy.
I took the form apart and painted
the side of the groove on each piece with a felt tip marker. I
started in filing with the board sliding on the top surface of the
form and the file working on the groove. With a few strokes I noticed
that there were high and low spots revealed by removal and
non-removal of the ink—not a surprising considering the results of
the measurements. I continued filing until all the ink was removed.
With the form reassembled, I measured again. The angles were much
better, the average being 59.98. The filing didn’t much
deepen the groove.
The final test was to make a couple of rods. The
result was what I hoped for, pretty much an end to the problems I was
having with dimensions and angles.