Dimension Compensation for Hollowing Bamboo Rods
by Mike McGuire
If a bamboo rod is hollowed without increasing its cross section
dimension, it wil be less stiff. To correct this the dimension must be
increased. Beam theory says that the stiffness varies with the cross
section moment of inertia.,
I0.
I0
= aD04
where D0
is the flat to flat dimension and a is a constant that
depends on the geometry of the cross section--hex, penta, quad
etc. Assumed in all this is scallop and dam hollowing with minimal length dams. If we hollow to a wall thicknes t, the new moment I1
is the moment of a solid rod of dimension D1
less the moment of what is removed by hollowing.
I1
= a[ D14
- (D1 - 2t)4 ]
To maintain stiffness
we have to have
I1
= I0
or
D14
- (D1
- 2t)4 = D04
The constant a divides out of the
equation. To get the correction, given t and D0
, we must solve for D1.
If we expand and rearrange this equation, we get
D13
- 3tD12
+ 4t2D1
- 2t3 - D04/8t = 0
This is a cubic equation in
D1,
that is it has the form
ax3 + bx2
+ cx + d = 0
where a = 1, b = -3t, c = 4t2,
and d = 2t3
- D04/8t.
As with quadratic equations, cubic equations can be solved with
formulas, but they are much more complicated.. As usual, Google is our
friend and if we ask it for a cubic solver, it comes up with several
choices. One that I like is at this link.
One calculates a,
b, c, and d,
puts them in, clicks the
enter button button and it will give you the
result.. Actually it will give you three results--the first of them is
the one we want. The other two are complex numbers which will also
satisfy the equation, but which don't apply here..From that page is a
link to another page which shows all the formulas involved in the
solution--not for the mathematically faint of heart.
Going through a
whole taper, calculating
a, b, c, and d
is a lot of work with a lot of opportunity for error.To get by that I
set this calculation up in a spread sheet so that I could calculate for
a whole rod in one shot. It then occured to me that it would be
interesting to look at the effects of hollowing on the Garrison stress
curve of the rod, so I added this to the spread sheet. This required
modification of some of the formulas to take account of the hollowing.
I will describe the details of this below. From this point, it wasn't
much of a leap think of using the stress curve of a solid rod to
calcluate the dimensions of a hollowed rod. This is much the same as
when one uses the stress curve to get dimensions of a new solid rod for
casting a different weight of line, as is implemented in RodDNA and
Hexrod. So this is part of the spread sheet now too. It is available
for download below. The main difficulty was that
another cubic equation turned up in going from the moment at a point on
the rod to the dimension.
Here are some results. The rod is a Garrison 212 casting 50 feet of 6
wt line. The hollowing is fairly conservative, the butt third has a
0.070" wall, the middle third 0.060", and the tip third not hollowed.
The results named "compensated" are the simple method where the moment of
inertia is held constant as described above. Hollow output stress is
when the rod is hollowed but no correction is done.
Position | Wall
Thickness | Input
Dimension | Cmpnstd Output Dimension | Stress Crv Output Dimension | Input Stress | Cmpnstd Output Stress | Hollow Output Stress |
0 |
| 0.0720 | 0.0720 | 0.0720 | 0 | 0 | 0 |
5 |
| 0.0840 | 0.0840 | 0.0840 | 193178 | 193178 | 193178 |
10 |
| 0.1040 | 0.1040 | 0.1040 | 208755 | 208755 | 208755 |
15 |
| 0.1220 | 0.1220 | 0.1220 | 199713 | 199713 | 199713 |
20 |
| 0.1360 | 0.1360 | 0.1360 | 198724 | 198724 | 198724 |
25 |
| 0.1490 | 0.1490 | 0.1490 | 195985 | 195985 | 195985 |
30 |
| 0.1620 | 0.1620 | 0.1620 | 190457 | 190457 | 190457 |
35 | 0.060 | 0.1750 | 0.1754 | 0.1756 | 183995 | 184434 | 185784 |
40 | 0.060 | 0.1880 | 0.1888 | 0.1891 | 177512 | 178094 | 180379 |
45 | 0.060 | 0.2000 | 0.2014 | 0.2016 | 174026 | 174602 | 177954 |
50 | 0.060 | 0.2120 | 0.2140 | 0.2142 | 171887 | 172347 | 176937 |
55 | 0.060 | 0.2280 | 0.2312 | 0.2314 | 162358 | 162777 | 168969 |
60 | 0.060 | 0.2400 | 0.2442 | 0.2443 | 161897 | 162016 | 169694Ö |
65 | 0.070 | 0.2540 | 0.2568 | 0.2557 | 157557 | 155689 | 160292 |
70 | 0.070 | 0.2660 | 0.2697 | 0.2682 | 157217 | 154755 | 160445 |
75 | 0.070 | 0.2800 | 0.2849 | 0.2829 | 153633 | 150706 | 157631 |
80 | 0.070 | 0.2960 | 0.3025 | 0.3000 | 147534 | 144284 | 152547 |
85 | 0.070 | 0.3100 | 0.3181 | 0.3150 | 145152 | 141401 | 150964 |
90 | 0.070 | 0.3250 | 0.3351 | 0.3312 | 141891 | 137676 | 148579 |
95 | 0.070 | 0.3400 | 0.3522 | 0.3475 | 139187 | 134461 | 146709 |
The differences from the solid rod are small where the hollowing
starts, becoming larger toward the butt. The corrections from the
stress curve are smaller than holding those from holding the moment of
Inertia constant. The weights for the input solid rod and various
amounts of hollowing are available from the stress curve calculations.
These are the weights of just the bamboo. No hardware is included.
Input
Weight | Hollow Output Weight | Cmpnstd
Output Weight | Stress
Crv Output Weight |
2.67 | 2.08 | 2.12 | 2.11 |
There is not a lot of difference between these curves with
the conservative hollowing. The picture changes if we hollow more
aggressively.
|
|
|
|
|
|
|
|
Position | Wall
Thickness | Input
Dimension | Cmpnstd Output Dimension | Stress Crv Output Dimension | Input Stress | Cmpnstd Output Stress | Hollow Output Stress |
0 |
| 0.0720 | 0.0720 | 0.0720 | 0 | 0 | 0 |
5 | 0.030 | 0.0840 | 0.0841 | 0.0842 | 193178 | 193469 | 194433 |
10 | 0.030 | 0.1040 | 0.1049 | 0.1052 | 208755 | 210247 | 215345 |
15 | 0.030 | 0.1220 | 0.1243 | 0.1249 | 199713 | 202598 | 213030 |
20 | 0.030 | 0.1360 | 0.1399 | 0.1409 | 198724 | 202581 | 218119 |
25 | 0.030 | 0.1490 | 0.1547 | 0.1560 | 195985 | 200449 | 220900 |
30 | 0.030 | 0.1620 | 0.1700 | 0.1715 | 190457 | 195216 | 220304 |
35 | 0.040 | 0.1750 | 0.1794 | 0.1786 | 183995 | 182483 | 194404 |
40 | 0.040 | 0.1880 | 0.1941 | 0.1930 | 177512 | 175559 | 190132 |
45 | 0.040 | 0.2000 | 0.2079 | 0.2063 | 174026 | 171519 | 188681 |
50 | 0.040 | 0.2120 | 0.2219 | 0.2199 | 171887 | 168839 | 188707 |
55 | 0.040 | 0.2280 | 0.2410 | 0.2386 | 162358 | 159355 | 182014 |
60 | 0.040 | 0.2400 | 0.2556 | 0.2524 | 161897 | 158272 | 183669 |
65 | 0.050 | 0.2540 | 0.2645 | 0.2577 | 157557 | 148787 | 163621 |
70 | 0.050 | 0.2660 | 0.2786 | 0.2706 | 157217 | 147513 | 164208 |
75 | 0.050 | 0.2800 | 0.2953 | 0.2859 | 153633 | 143378 | 161942 |
80 | 0.050 | 0.2960 | 0.3146 | 0.3038 | 147534 | 137075 | 157445 |
85 | 0.050 | 0.3100 | 0.3318 | 0.3193 | 145152 | 134094 | 156251 |
90 | 0.050 | 0.3250 | 0.3505 | 0.3362 | 141891 | 130354 | 154235 |
95 | 0.050 | 0.3400 | 0.3695 | 0.3531 | 139187 | 127109 | 152671 |
Since more correction is required it is not surprising to see
larger dimension differences from the solid rod.
Input
Weight | Hollow Output Weight | Cmpnstd
Output Weight | Stress
Crv Output Weight |
2.67 | 1.58 | 1.69 | 1.58 |
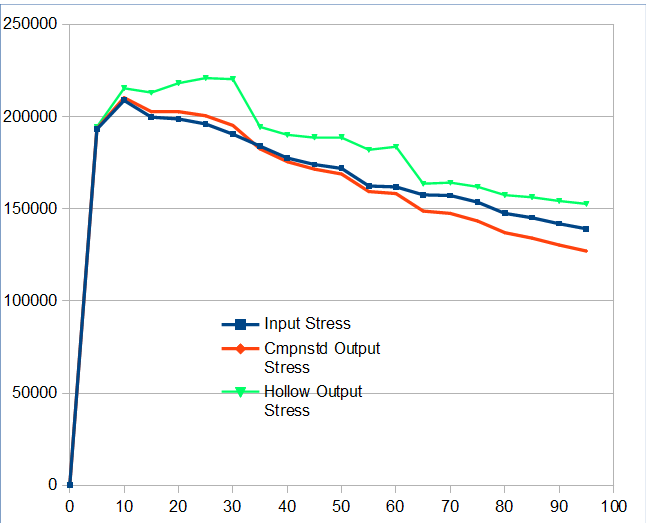
The stress curve (green) of the uncorrected hollowed rod is getting a
bit wild here.
The Spreadsheet
Below
is a picture of part of the input/output sheet. To use it enter the rod
parameters in the yellow line. The number of pieces can be 1, 2, 3, or
4. The truncation factor can be 1, 0.75 or 0.66. The station
spacing can be whatever is the spacing of the input taper. The position
values are automatically calculated from the length and the spacing.
Leave the wall thickness blank where no hollowing is done. Otherwise
don't make it greater than half the input dimension. The input taper
can be copy/pasted from another app such as RodDNA or Hexrod. After all
the input data is in place, enter 0 in the Reset box, push return, then
enter 1, push return. This correctly initializes and then runs the
iterative process that calculates the hollowed taper from the stress
curve of the input taper. Depending on the previous contents of the
sheet, garbage may appear as data is entered. The reset process should
clean this up The graph of the stress curves appears to the right
of what is seen below.The spreadsheet is protected This means only the
input cells can be changed. This protects against accidental damage.
There is no password on the protection. It can be removed at the users
own risk if you want to tinker with it. It can be downloaded from the
link below.
New version correcting errors as of 7/8/17
Solid2Hollow.xls
Modifications of Garrison Stress Curve Formulas
For calculating a stress
curve the rod is divided into segments, typically the 5 inch segment of
the taper. The weight of each segement must be calculated. This is formula
III on page 251 of Garrrison.
W = 0.668 (h/3) [A + sqrt(A A1) + A1]
Wher A is the area of
the big end of the segment and A1
is the area of the small end,
h is the length,0.668
is the density of bamboo. This actually can be simplified a little by
noting that the area in terms of the flat to flat dimension D
A
= sqrt(3)/2 D2
then we have
W
= 0.668 [h / 2sqrt(3)] (D + DD1
+ D12)
where D is the dimension
of the big end and D1
the small end, sqrt
means square root. When we hollow, we must subtract off the weight of
what has been removed so we have
W
= 0.668 [h / 2sqrt(3)] (D2 + DD1
+ D12-
d2 -dd1
- d12)
where d is the hollow dimension at the big end, d1 at the small end.
The location of the center of gravity C relative to its big end is required. This is formula IV on page 251.
C = (h/4) [A + 2sqrt(AA1) +3A1] / [A + sqrt(AA1) + A1]
again it can be simplified in terms of the dimension
C = (h/4)(D2 +2DD1 + 3D12) / (D2 + DD1 + D12)
When we hollow it becomes
C = (h/4)(D2 +2DD1 + 3D12- d2 - 2dd1 - 3d12) /
(D2 + DD1
+ D12-
d2 -dd1
- d12)
Finally we have to deal with formula VI on page 258. This is the relation between moment at a point on a rod, the stress value, and the dimension. Garrison gives us.
D = (M / 0.120 f)1/3
Where M is the moment and f is the stress. If we solve this for the stress, we have
f = M / (0.120 D3)
To deal with hollowing we have to go back to a more general equation for the relation.
f = MD / 2I
Where I is the cross section moment of inertia. For a hexagonal cross section it is
I = [5 / 48 sqrt(3)] D4 = 0.06014 D4
if we put this into the general equation
f = M / (0.12028 D3)
having divided out a factor of D we get what Garrison gave us. If we hollow I becomes
I = 0.06014 [ D4 - (D - 2t)4]
where t is the wall thickness and the stress formula is
f = MD / { 0.12028 [ D4 - (D - 2t)4 ] }
This is no problem for calculating the stress, we know M, D, and t. But if we know f, M, and t and want to find D, we have another cubic equation to solve. So rearranging the above equation, we get
D3 - 3tD2 + [4t2 - M / (8 x 0.12028 f t) ] D - 2t3 = 0
When
we are getting a taper from the stress curve we have to solve this
equation for every station of the taper, multiple times as we converge
on the final value. This is built into the spreadsheet as is the
solution of the cubic for the simple conspensation for hollowing.