An Implementation of a Baginski Beveler
by Mike McGuire
The idea of a Baginski beveler was described for the bambo rodmaking
community by Tim Anderson in
Power
Fibers 36.
He described several approaches one might
take to implementing it. Tim has graciously allowed me to include a
copy of his article, downloadable from a link at the bottom of this
page. Here I am describing in detail one using a
6"
Harbor Freight Bench Grinder that turned out pretty nice.
UPDATED DESIGN I have replaced the anvil arm with a dovetail arrangement.
See Below.
It turns out to be quite easy to remove a grinding wheel and its sheet
metal shield and attach baseplate for the beveler using the mounting
holes for the shield.
The mounting screws are 10-24 thread. The shaft is 0.500", stepping up
to 0.585". If you do this on the left end of the grinder,
don't lose
the shaft nut--it's a left hand metric thread 12-1.5.
Making the wheel.
The most difficult part to make is the wheel. For that one needs a
lathe, but not much of one. It was at the limit of the capabilities of
the 7 X 10 Harbor Freight Mini-Lathe I have, but possible. The outside
jaws of the chuck will hold a 3" diameter piece at maximum. This turns
out to be about as large as you want to go with this grinder--it will
lug down if one tries to feed a strip too fast. I have in mind making
some two-hand rods which will require big strips so I decided I wanted
a depth of the Vee-groove of 0.5". Now the outside jaws of the chuck
are about 0.25" deep and the half width of a 0.5" groove is 0.288", so
the starting point would be a couple of aluminum discs 3" diameter by
5/8" thick to clear the jaws while cutting the bevel. These I got from
Online Metals for about $7 for the two. What they do when
they make a specified cut is guarantee one will get at least the
minimum and up to 1/8"
more. The price was mostly the cost of cutting. The cuts were pretty
smooth and did not require deep facing cuts to clean up.
So what I did was first face both sides to about 0.600 thick, and bore
a 0.500 hole through the center
Accurately measuring the depth of the bevel as it's being cut
is a problem, so I registered a sharp pointed bit at the edge, moved it
0.500" in accurately with the cross feed and marked a circle of the
diameter where the bevel would be done. On the second disk, I copped to
the idea of painting the disk with a felt pen before making the mark to
enhance contrast. Unfortunately the swarf from cutting the bevel
pretty much scrubbed it off. Probably good layout dye would have worked
better.
Cutting the bevel requires moving the cutting bit with the compound set
to 30 degrees from the cross slide direction. There is an angle scale
on the lathe but it doesn't go that far. However it's easy to do with a
30-60-90 drawing triangle.
The bevel is cut by moving the cross slide in a few thousands, and
moving the compound through the range where it cuts. It was possible to
cut going both in and out with the compound. When I got close to the
limit line, I made the cuts just from inside.
It's
probably not necessary, but to lighten the wheel, it can be mounted on
a 1/2" bolt and faced down to the diameter of the washer underneath the
nut. To get good concentricity there, I bored a couple of 7/16" washers
to 1/2". When the cut is done, there is a boss there at the original
thickness.
Tim
Anderson had an alternate approach to holding the disks with
a
faceplate arrangement he made. This enabled him to cut 4 inch diameter
disks on a similar lathe system to mine. However 3 inch diameter disks
are about the maximum the grinder I used will handle without stalling.
He uses a large router which can handle the 4 inch disks.
Gluing the Abrasive on.
The
surface to glue the abrasive to is technically speaking the frustrum of
a cone. There is a discussion of this geometry and the formulas needed
for setting up a strip that will lay flat on the surface without
wrinkles at this
link.
Reduced to the situation at hand one draws two concentric circles on
the back of the sandpaper with a compass. For the 60 degree
setup
we have here the inner radius is 1.155 times the inner radius
of wheel and the outer radius is 1.155 times the outer radius of it. A
48 degree pie slice out of it will have the ends just meeting without
overlap. For a quad strip beveler, the factor would be 1.414 with a 105
degree slice, and for a penta strip beveler the factor would be 1.236
with a 69 degree slice.
I have used epoxy, Barge cement (contact
cement) and adhesive backed sandpaper and the all worked fine. Heating
the disks with a head gun works for getting off worn out paper.
Adhesive backed sandpaper here.
Setting Up the Beveler
The
beveler is set up on a 5" x 10" x 3/8" red oak baseplate. The
sheet metal shield can be used as a template for locating the
mounting holes.
The
tricky part is getting it level. After making sure
the
grinder was sitting level, I used a level to draw a line on
the
shield which I transfered along with the mounting holes to the
baseplate. I got it close but not quite right.
The
in feed and out feed shelves shout be in line with the groove
in
the wheel and level--it's not level in the picture. Use a triangular
strip laid in there to locate these.
UPDATED DESIGN I have replaced the anvil arm with a dovetail arrangement.
See Below.The
anvil bar should be set so the top is level when cutting about the
smallest dimension strip wanted. It pivots on a 1/4-20 bolt, and is
spaced out with nuts and washers to be centered on the wheel. Use the
wheel itself to cut the contact area at the wheel, but leave some flat
edge, don't cut it sharp. The other end is to be clamped with a 1/4-20
bolt the moves in a slot, also with nuts and washers for spacing.
I turned a pencil down to fit in a 1/4" hole and scribed the
arc
of the slot and then drilled an filed the slot out. There are
clearances cut on the input and output side of the anvil. The picture
at the top of this article shows a piece of metal scale and a pointer
for reproducing a strip size. The rest of it is a matter of
building an enclosure so that a shop vac can effectively collect the
dust.
Using the beveler
The strips need to have their
nodes well flattened and be reasonably straight. While soaking the
strips makes flattening nodes easier, dry them out before beveling.
Wet strips will rapidly clog the wheels. Wear gloves while
handling the strips--the edges get sharp. Keep a good hold on a strip.
If you don't it will launch a strip back out clear across the room.
While you can do a strip in one pass it seem better to take two or
three to get to desired dimension. If you jam a strip in too fast, it
can stall the grinder. If this happens, back off a bit while it comes
back to speed, and feed
in more slowly. When cutting extra wide strips, say for the butt
section of a spey rod, the spacing between the wheels will need
to be widened with a washer or two so the strip fits between the wheels
for the first cut or two.
After
some number of strips have been beveled, the abrasive will become
clogged with resin from the bamboo and not cut as efficiently.
The fix is to clean it rather than replace it. There are resin
and gum removers available form woodworking retailers. I got some
very effective stuff from
Woodcraft.
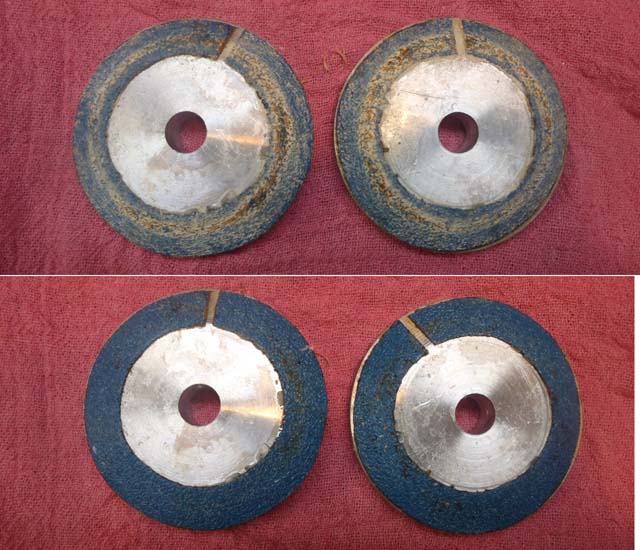
Wheels before and after cleaning.
Link to Tim
Anderson's beveler articleUPDATED DESIGN Dovetail Anvil
On of the cutter wheels is removed to show the cut on the anvil.
The carriage bolt through the anvil clamps it in place. The screw
thread sticking up is for seeting the dimension.
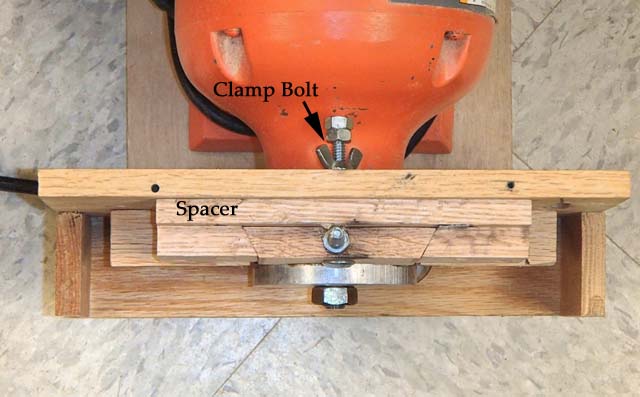
Top view: the thickness of the spacer is adjusted to center the anvil over the wheel.
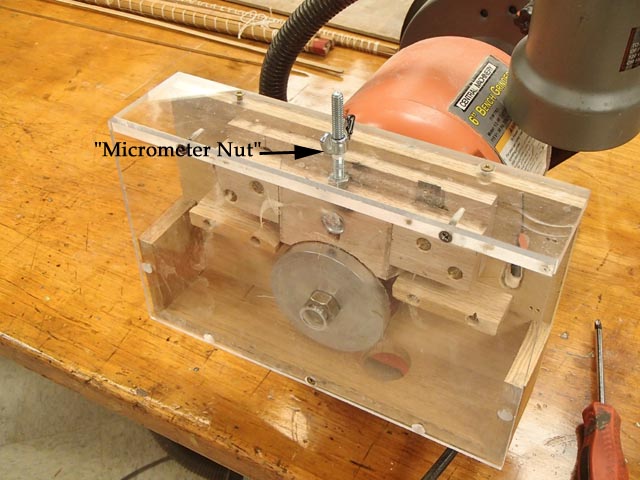
This
is what it looks like all assembled with dust cover. The
"micrometer nut:" is a nylon insert wing nut so it stays put wherever
set. It's a 1/4-20 thread, so one 360 rotation moves the anvil 0.050
inches. Zero it by putting it in contact with the wheel while
micrometer nut is in contact with the case. Tturn it to desired
dimension and set clamp bolt again making sure the
micrometer nut is flush with the case. It's not high precision--check
with cut on a piece of scrap material.